Robotically Wound Carbon Fiber Truss Modules
Partner: Jiansong Yuan
Location: Weitzman School of Design UPenn - Philadelphia, PA
Studio: Material Agencies directed by Ezio Blasetti
When: Fall 2020
How can we embed fabrication and assembly intelligence into a high-performance material? What new material relationships emerge through unexpected combinations? In this project, pre-preg carbon fiber strands are robotically wound around a custom jig assembly to create novel modular truss systems.
Assembly
The prototypes were developed in rapid succession through an inexpensive customizable jig system. The design goal was to create a three-dimensional winding process that performs structurally and tectonically, replacing the need for standard complex weaving machines. The jig needed to be robust enough to hold the tension of the carbon fiber and created through an inexpensive means of production for truly rapid prototyping.
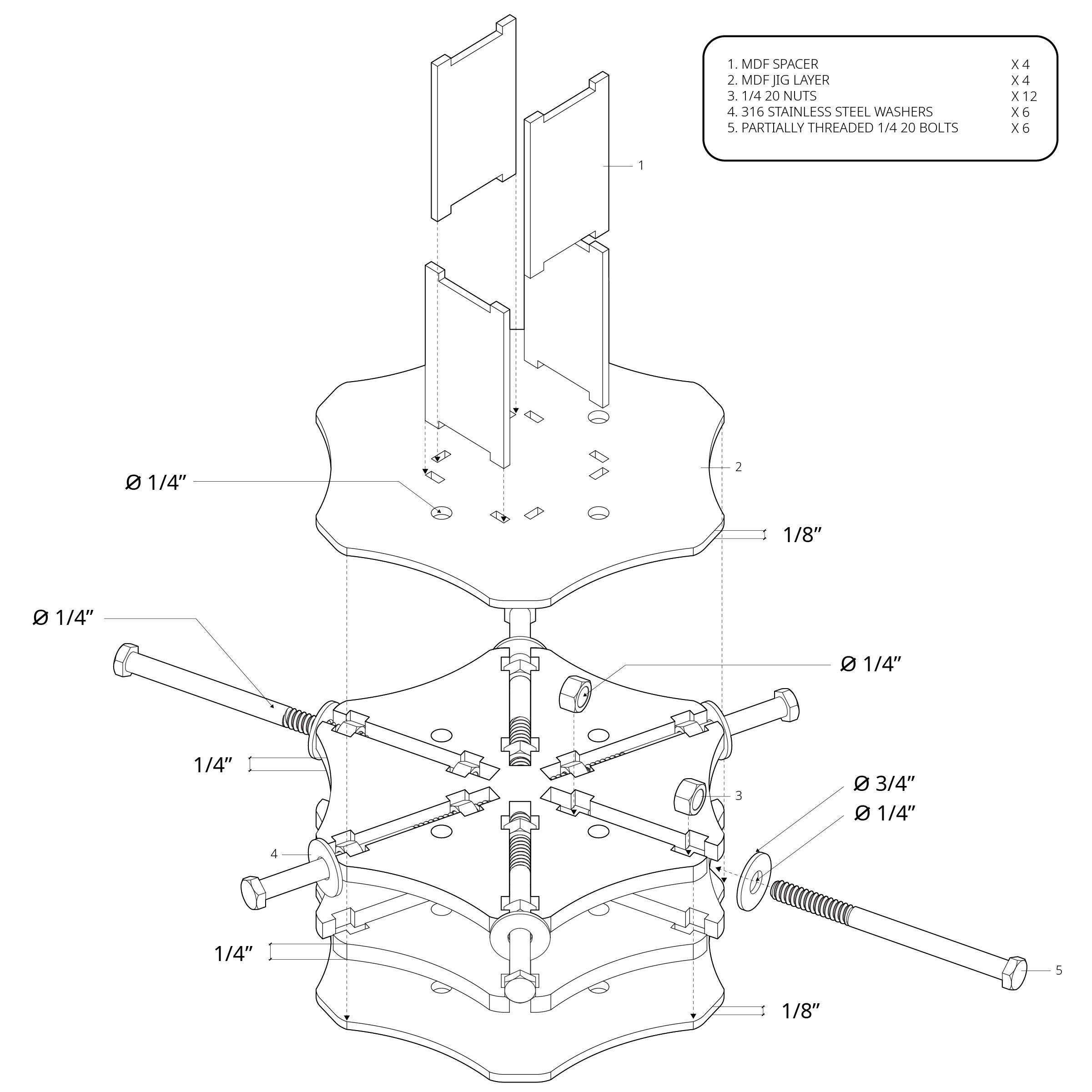
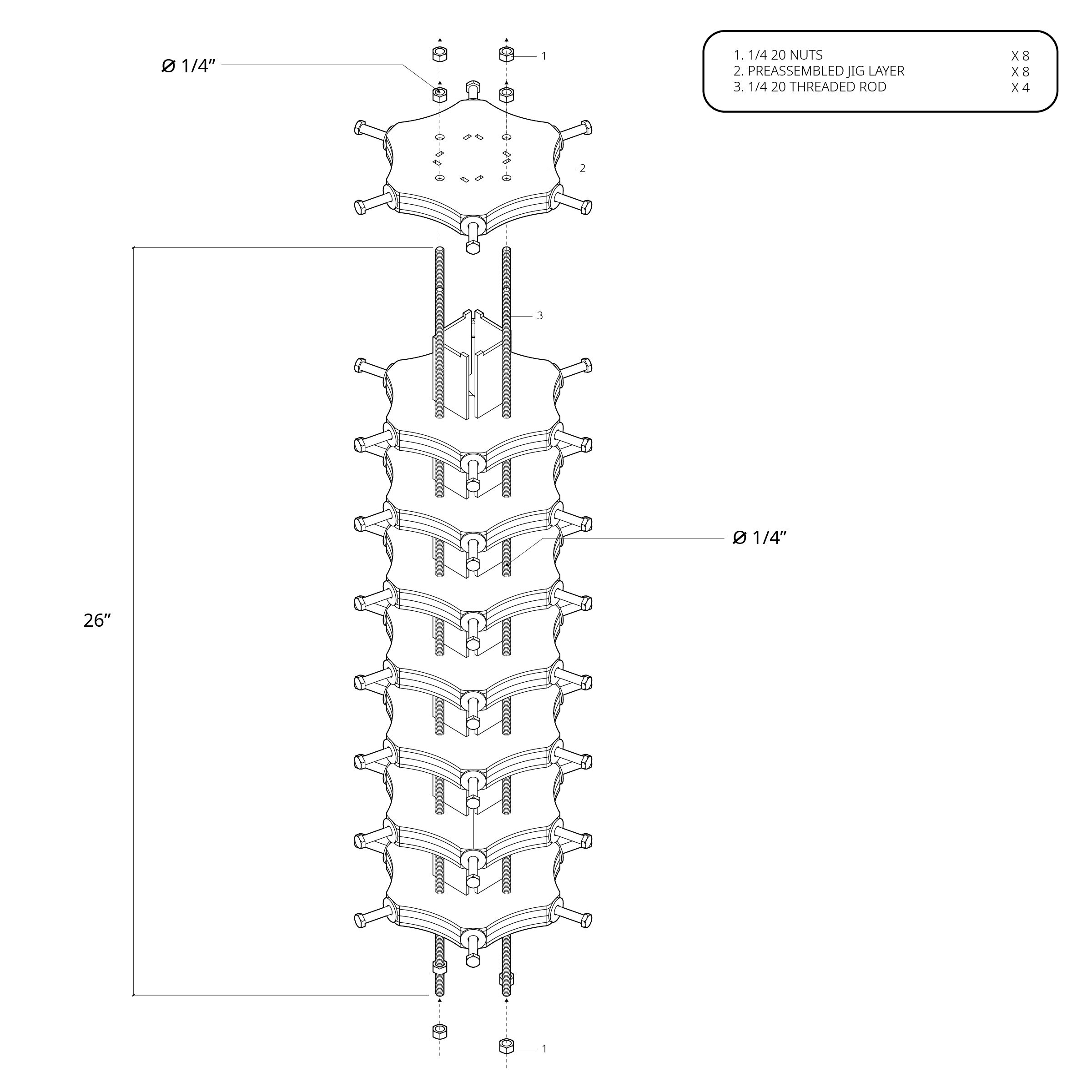
Flexible
The semi-stiff nature of half-baked carbon fiber, combined with a specific weaving pattern, gave us extreme flexibility in the module. In a two-step winding process, we were able to bend the fiber truss system up to 180 degrees over the length of three feet.
modular
The fabrication of wound fiber relies on a peg (1/4” steel bolt) for the fiber to wind around. The prototype makes this fabrication necessity a design consideration and uses the peg hole after the fiber has been hardened as a means for assembly and connectivity.
variable
The combinatorial possibilities vary dramatically, as demonstrated with only a few prototypes.
fiber + hempcrete prototypes
To expand upon the carbon fiber truss system, we theorize that a multi-material relationship will need to be developed to fully realize the system’s potential. Hempcrete was a natural translation for our experimentation, as an inherently unstable medium that requires a formwork and secondary structure to form to. The carbon fiber can act as both the formwork and the structural system while allowing the hempcrete to provide surface and insulative properties. The work presented here is a very preliminary study, meant to open up new ideas on material combinations.
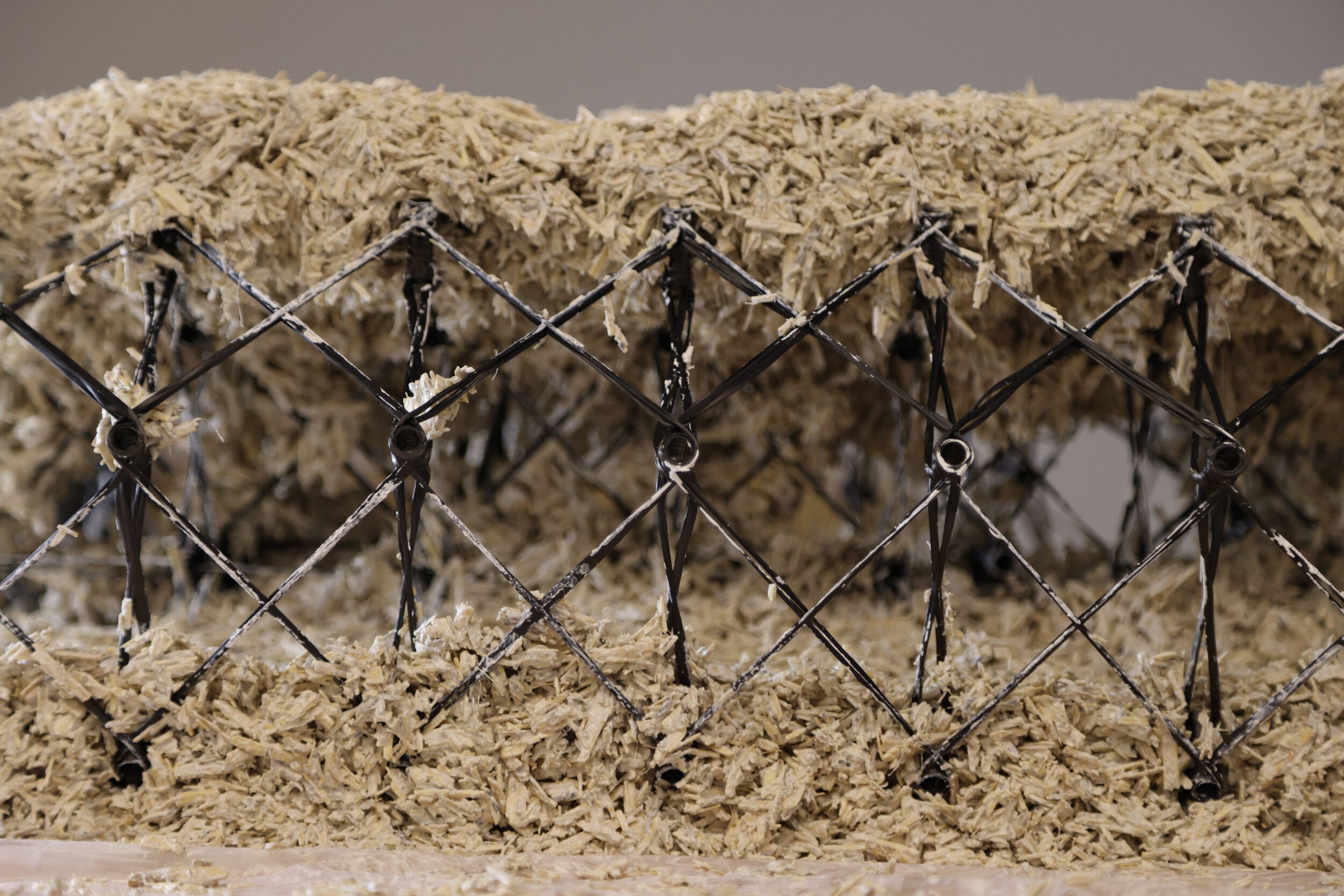
Special thanks to:
My partner, Jiansong Yuan
LimeWork US / Anthony Hita